|
THERMAL PERFORMANCE TEST
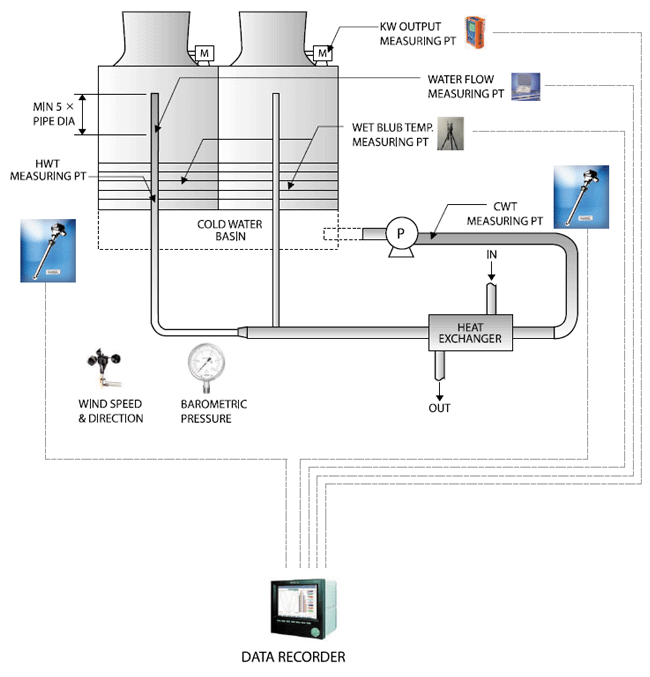
For a thermal performance test, there are certain site requirements
that need to be met by the customer. The following list includes
the common considerations for a standard tower installation
operating on a cooling water system.
1. Taps should be installed for measurement of water temperatures
if required. Hot water temperature shall be measured in the
riser pipes. The cold water temperature is normally accomplished
at the discharge of the circulating water pumps. The most
common location is at the pressure gauge tap present on most
systems.
If this is not available or applicable on a system, special
taps or another solution must be identified. Measurement in
a tower basin is not acceptable. Measurement of cold water
temperature in a flume or channel can sometimes be accomplished
with acceptable accuracy, but specifics should be reviewed.
2. Power for test instruments available adjacent to the tower.
This should be single phase, 2200 volt, 60 cycle.
3. The tower should be ready for testing before the test engineers
arrive. The following considerations are important to evaluate
the full capability of tower:
a. Towers with PVC film-fill should be operated at design
water flow and heat load for 1000 hours prior to doing a performance
test. The reason for this is to wash lubricants used in the
production of the PVC from the surface of the fill and to
protect the separation of water from the surface of fill due
to the surface tension. These lubricants inhibit the wetability,
and heat transfer capability of the fill.
For additional information refer to the Cooling Technology
Institute paper TP00-01 - "Design Features of Cross-Fluted
Film Fill and Their Effect on Thermal Performance". The
work shows that film fill requires about 2 to 3 weeks of seasoning
in their "aging tank". They indicate that one week
in the aging tank was equal to about four weeks of tower operation,
which means about 8 weeks (1344 hours) of seasoning time in
the tower to get the full capacity of the fill performance.
b. The tower should be clean. The water distribution system
should not have any damaged, missing, or plugged nozzles or
orifices. The water distribution system should be balanced
between the cells. The air inlet should be cleared of any
blockage. If the tower has adjustable louvers, they should
be in the normal design position. The eliminators should be
free of foreign matter. Fan discharge should be clear and
unobstructed.
c. Water flow and heat load to the tower, or representative
cells, should be as close to design as the system will permit.
If the code recommended limitations cannot be met, all parties
should review the situation to agree on the deviation or delay/cancel
the test.
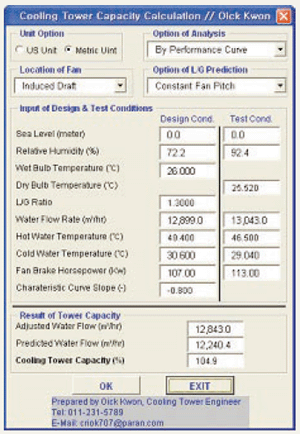 |
d.
Any water by-passes should be closed and inspected to
ensure there is no leakage..
e. Any source of air leakage should be closed/blocked.
Examples: access doors, or holes in the casing or fan
cylinders.
f. All fans must be operated on full speed forward during
the test period.
g. The owner or his representative should appoint an
electrician or qualified operator available to assist
in the measurement of fan power on mechanical draft
towers. A wattmeter is normally used to measure fan
motor power at the starters or other suitable location.
h. All parties to the test should be advised in advance
of any special safety issues required at the site. This
includes training, equipment, testing, or restrictions.
|
|
|