1) Definitions
These leaks are usually referred
to as emissions or releases. They are simply inadvertent
discharges of either chlorine liquid or vapor into the
surrounding atmosphere. There are both minor and major
leaks. When liquid chlorine is involved, the leak is
almost always major.
Minor leaks usually
occur at the start-up of a new installation or right
after maintenance or inspection procedures. They usually
are the result of a gasket failure, valve packing adjustment,
or equipment malfunction.
Major leaks are generally
referred to as catastrophic leaks. They include such
things as container rupture, guillotine break in a pipe
line under pressure, broken flexible connection, fusible
plug failure, and/or repair work while a system is under
chlorine supply pressure. Not to be overlooked is the
real possibility of spontaneous combustion of steel
and chlorine if the temperature reaches 483oF
for some reason.
2) Frequency and Magnitude
of Chlorine Leaks
A list of the chlorine accidents
reported to the Chlorine Institute over the past 50
years indicates by frequency and magnitude of chlorine
emission. The following category of causes is in order
of potential hazard:
- Fire
- Flexible connection failure
- Fusible plug failure
- Freak accidents caused
by carelessness and ignorance
- Valve packing failure
- Piping failure
- Equipment failure
- Container failure
- Chlorine pressure gages
(1) Due to Fire
Fire was listed by the Chlorine
Institute as the most serious hazard primarily because
companies that stored swimming pool chemicals were often
wiped out when stored granular hypochlorite suffered
a spontaneous explosion. If 150-1b cylinders of chlorine
were in the area, these too would explode because the
fusible plug melts at a few degrees after the cylinder
becomes skin-full. Ton containers are different. When
they become skin-full, the dished heads blow outward
without rupturing the container. This maneuver increases
the volume of the container which is sufficient to allow
the necessary expansion of the chlorine during the next
4oF rise required for the fusible plug to
melt. Fortunately, such fires as described above do
not happen in water or wastewater treatment plants.
Moreover, the plants that use modern chlorination or
sulfonation equipment handle these vapors under a vacuum
so that excessive pressures, for whatever reason, rarely
if ever occur.
In the early years of ton
container usage, the industry suffered container explosions
due to the spontaneous combustion of nitrogen trichloride
(NCl3). When chlorine is made from electrolytic
cell water containing ammonia N in sufficient quantities,
the chlorine produced will contain NCl3, which is soluble
in liquid chlorine. When the liquid is withdrawn, the
NCl3 evolves as a vapor and will explode.
This first occurred at a New York City water treatment
plant in the 1920s. It became a simple matter to remove
the ammonia N from the cell water, but Americans did
not do a very good job of exporting this information.
In 1981, there were such explosions at the plant of
local chlor-alkali located Bogota, Colombia, and S.A.
It was reported that more than a dozen U.S.-made ton
containers with their dished heads still intact although
they had been blown from a concave to a convex position.
There never has been any
report of a container failure of 150-1b cylinders &
one-ton containers at any potable water, wastewater,
or industrial cooling water chlorination or sulfonation
installation in the United States or Canada. Fires in
these locations are practically unheard of. If a fire
were to occur that caused a major liquid chlorine release
it would be vaporized immediately and would disappear
in the chimney effect of the fire.
(2) Due to Flexible Connection
Failure
Probably the most frequent
cause of chlorine emissions resulting in overexposure
to personnel is the failure of connecting lines between
the container and the metering and control equipment.
These connecting lines are traditionally made of annealed
copper, 2000 psi strength, and cadmium plated. Copper
is used because it is flexible and has the proper structural
strength; however, at each container change, the chlorine
remaining inside the tubing will absorb moisture from
the atmosphere, and a cycle of corrosion will begin.
Therefore, any flexible connection has a life dependent
upon how many times it is disconnected and left open
to the atmosphere. To check the worthiness of a flexible
connection, bend it carefully; if it screeches slightly,
it is due for replacement. The noise produced by the
bending is indicative of the magnitude of corrosion
products on the inside of the tube.
(3) Due to Fusible Plugs
Failure
Fusible plug failure without
any evidence of elevated temperature caused by fire
or direct sunlight is next in order of hazard magnitude.
A fusible plug which is supposed to melt at 158? may
leak from corrosion or a poor bond between the lead
alloy and the plug retainer. There is only one fusible
plug on a 150-1b cylinder, at the base of the outlet
valve . There are three in each of the dished heads
of a ton container. Gas emissions through faulty fusible
plugs have been numerous enough to question their safety
value.
(4) Due to Freak Accidents
caused by Carelessness and Ignorance
Carelessness is high on the
list of causes of chlorine accidents, sometimes involving
unusual situations. One case involved a 6-inch buried
chlorine gas line originally and entirely within the
property of two chemical plants. Adjoining property
became subdivided 20 years later, and some of the underground
piping, including that for chlorine gas, became part
of the pavement area of new streets. This chlorine gas
line was first cut into by mistake by a welder who was
supposedly inactivating obsolete natural gas lines.
The heat from the torch burned a small hole in the pipe,
so that the chlorine could support combustion of the
carbon steel pipe. Within seconds, the hole was approximately
8 inches in diameter, resulting in an almost immediate
discharge of the contents of 7000 feet of 6-inch pipe.
A few months later, on successive days, this same line
was broken twice again by a backhol excavating for additional
underground lines. After these experiences, the decision
was made to lower the pipe from its former depth of
approximately 2 ft to approximately 5 ft.
(5) Due to Valve Packing
Failure
Valve packing failures have
never caused any serious problems. If the leak is minor,
it can often be corrected by tightening the packing
nut. Serious leaks are taken care of by the application
of a proper container safety kit.
(6) Due to Piping Failure
Piping failures have been
rare, and are sometimes the results of using improper
materials. Lines carrying liquid chlorine can be a potential
hazard. One of the few fatalities attributed to chlorine
in recent years was caused by the failure of a liquid
chlorine line. The worker's death was the result of
his constricted breathing caused by the amount of chlorine
fumes, which made it impossible for him to climb out
of the confined location of the leak.
(7) Due to Equipment Failure
Equipment failure usually
refers to vaporizers used between the containers and
the chlorine metering and control equipment. These failures
are due primarily to corrosion by the chlorine, and
are a function of the amount of wall thickness versus
the amount of chlorine passing through the vaporizer.
The frequency of this type of accident is low.
(8) Due to Container Failure
Container failures, except
those caused by fire, are rare. The chlorine packagers
through-out the United States and Canada are keenly
aware of the potential hazards of handling chlorine
containers. This has resulted in a strict monitoring
of container condition. Perusal of the Chlorine Institute
accident reports indicates two container failures over
a period of 15 years. Considering that shipments in
150-1b and ton containers amount to nearly 100,000 per
year, this sort of accident is a rarity and is usually
a result of using an over-age cylinder.
One of these accidents occurred
at a military base. A ton container was being loaded
at a dock. It slipped out of the sling and fell on its
end. The tank split at the "chime," which
is the joint between the container and the dished head.
Investigation of this accident revealed that this container
had been in service by the military for 45 years.
(9) Due to Chlorine Pressure
Gauge
This type of gage is vulnerable
to leaks because of the silver or hastalloy diaphragm
that protects the brass Borden tube. The Borden tube
flexes to indicate pressure changes. Constant flexing
of the diaphragm causes metal fatigue that results in
diaphragm failure. When this occurs, the brass Borden
tube corrodes quickly from the inherent moisture in
the chlorine. This results in a severe leak. These gages
should be replaced about once every five years.
3) Calculating Chlorine Leak
Rates
All of the following calculations
are based upon the Chlorine Institute formula shown
in its Pamphlet No. 74 (1982) under 2.4.1, "Release
rate Formulas."
(1) Liquid Release

Where:
A = area of opening to atmosphere, ft2
P1 = upstream pressure, psi
P2 = downstream pressure, psi
r = density of liquid chlorine upstream from the opening
to atmosphere, lb/ft3
(2) Vapor Release
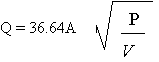
Where:
A = area of opening to the atmosphere, ft2
P = upstream pressure, psi
V = upstream specific volume (1/r), ft /lb
To be continued.
Please press the next button.... |