(3) Guillotine Break in a Pipeline
Ton Container Supply:
The maximum size of a chlorine header system under pressure
in any applications should never be larger than one
inch. If the installation involves liquid withdrawal
from ton containers, then evaporators will be an integral
part of the chlorine supply system. Therefore, the worst-case
scenario would be a rupture in the liquid header between
the containers and the evaporators. To simplify the
concept let the calculations be confined to one container,
one evaporator, and 100 ft length of one-inch header
pipe in the length.
The liquid exiting the container
must pass through a 3/8 inch tubing in the dished head
-then through the container shutoff valve, then through
the auxiliary container shutoff valve, and finally through
the header valve. All of these components are flow restrictors
compared to a one-inch pipe. So how can these restrictions
be accounted for in calculating the chlorine leak rate?
Circa 1950, the operating
personnel needed to know the maximum possible liquid
withdrawal rate from a single ton container, at the
East Bay Municipal Utility District wastewater treatment
plant, Oakland, California. Their Chlorinator capacity
was 18,000 lb/day. Their test, which they performed
several times, indicated that the maximum rate was only
about 10,200 lb/day. The pressure drop between the container
and the entrance to the chlorinator was on the average
about 85-40 psi = 45 psi because there was a pressure-
reducing valve between the evaporator and the chlorinator.
The flow at this pressure drop has to be recalculated
to reflect a zero pressure at the leak. To apply a worst-case
situation, let us assume a container pressure of 120
psi.
Using the Chlorine Institute
formula:

Where:
Q = 10,200 lb/day = 0.1181 lb/sec
r = 88 lb/ft3
Substituting this in the
above formula, the value of the unknown, 77A, can be
found:

Q = 0.1181 lb/sec = 77A x
62.93
77A = 0.00188
Assuming a cylinder pressure
of 120 psi, chlorine density at 88 lb/ft and substituting
77A = 0.00188 in above equation, the leak rate Q will
be:

Q = 0.1899 lb/sec x 60 =
11.4 lb/min
This then is the worst-case
leak rate from a single ton container "on-line",
when there is a guillotine break in the liquid chlorine
header piping. It is obvious that if ton containers
are being used for liquid withdrawal, an evaporator
is part of the system. Therefore, when there is a guillotine
break in the liquid header, the contents of the evaporator
becomes part of the leak.
Powell found by actual test
that the maximum liquid withdrawal from an inverted 150-lb
cylinder was 20 lb/min at 90 psi cylinder pressure.
The restrictions in this instance were the cylinder
valve and 3-4ft of 3/8 inch tubing.
All chlorine evaporators
are designed to vaporize at a temperature variation
between 160 and 180oF, regardless of the
chlorine feed rate. This means that the level of liquid
chlorine in the evaporator remains fairly constant.
It is safe to conclude that the evaporator content is
never more than 100 lb. At 20 lb/min., the evaporator
will empty in about 5 minutes because of the chlorine
header rupture. Therefore, the probable maximum chlorine
release rate will be 11.4 + 20 lb/min. for the first
5 minutes and then 11.4 lb/min after that interval.
This is for each ton container "on line" and
each evaporator.
Such a leak will cool the
room so quickly that vaporization is temporarily stopped.
During this time, if the container floor area has been
designed properly, the liquid chlorine will flow through
the collecting slots in the floor and be hustled off
to the scrubber system. This reduces enormously the
amount of time required to clean up a major spill. This
maneuver capitalizes on one of the little-known properties
of liquid chlorine-its solubility in water. Under a
slight pressure, such as the discharge from an eductor
or pump, its solubility is 3 to 4 times that of chlorine
vapor.
(4) Ton Container Flexible
Connection Failure
Assuming a worst-case situation,
the flexible connection breaks at the auxiliary container
valve. Logic dictates that for a 120-psi cylinder pressure
without the restriction of a header valve plus a 4 ft
flexible connection, the release rate will exceed the
rate from a header pipe rupture. A reasonable estimate
would be a 20 percent increase: 11.4 x 0.2 = 13.68 1b/min.
(5) Fusible Plug Failure
from Corrosion
A. Description
This is the most common problem
of fusible plug failure. A 3/4-inch plug contains a
lead core about 3/16 inch in diameter in a brass body.
The inherent moisture in "dry" chlorine begins
an immediate attack on the vulnerable brass body. Therefore,
the hole generated by the corrosion is shaped like a
cone with the base of the cone on the inside of the
ton cylinder. The end result of this corrosive attack
leads to a pinpoint hole between the brass body and
the threaded steel of the dished cylinder head. Field
observations indicate that this hole is never larger
than 0.1 inch in diameter.
B. Liquid Release
For a worst-case situation
the following calculations will be based upon a hole
diameter of 0.15 inch, with the fusible plug located
below the chlorine liquid level in the ton container.
Here again the container pressure is assumed to be 120
psi.
Therefore:

A = PI x D2 /
4 = 3.1416 x (0.15)2 / 4 =0.018 in2
A = 0.000125 ft2
Q = 77 x 0.00125 x (120 x 81)1/2 lb/sec
Q = 77 x 0.00125 x 98.59 = 0.949 lb/sec
Q = 56.94 lb/min
C. Vapor Release
This is an important comparison
because knowing the huge difference in the release rate,
the safety crew should attempt to rotate the leaking
plug to the vapor area. If this is done, the escaping
vapor will cool the liquid to 40oF in 3-4
minutes. This has to be taken into account when using
the Chorine Institute formula:
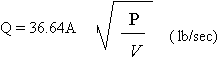
The container pressure will
have been reduced enormously because the escaping vapor
is at zero gage pressure. There is little doubt that
the container pressure will be as low as 40 psi. Then
V will be chosen for the density of chlorine vapor at
40 oF, which is 0.77 lb/ft.
Then:
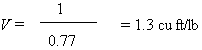
Therefore:

Q = 1.52 lb/min
D. Fusible Plug Blow-out
There is no such occurrence
on record but it always remains a possibility. This
is almost equivalent to a container rupture. It is assumed
that the total discharge will be liquid chlorine. The
container pressure will drop dramatically in the first
few seconds, similar to a flash-off. For the sake of
a rational calculation it will be assumed that the container
pressure drops to 30 psi. This is equivalent to a liquid
temperature of 20oF; therefore, the density
of the liquid chlorine is 93 1b/ft. So the leak rate
is calculated as follows;

r = density at 20oF
= 93 lb/ft3
A = PI x D2 / 4 = 3.1416 x (0.75)2
/ 4 = 0.44 in = 0.003 ft2

Q = 732.09 lb/min
It is quite obvious that
the calculations indicate an impossibility. The contents
of the container could never be discharged at that rate;
otherwise the container would be empty in less than
3 minutes! The scenario that is closer to what will
happen is a sudden cooling of the liquid chlorine that
brings the container pressure to atmospheric, whereby
the liquid chlorine will go into a freezing and thawing
cycle that may take hours for the chlorine to escape.
4) Summary of Catastrophic
Leak Events
- Whenever there is a major
leak, the flash-off phenomenon will always prevent
a positive pressure condition in a containment structure.
The sudden vaporization due to flash-off cools the
closed area so fast and so much that a negative pressure
in the room is the result.
- There will always be
a significant amount of liquid chlorine that must
be dealt with as soon as possible. Because it much
more soluble in water than chlorine vapor, it can
be disposed of quite easily by a water-operated eductor
or a liquid chlorine pump.
- The only way that liquid
chlorine can be cooled by a leak is to withdraw vapor
from it. Liquid flowing out of container due to a
major leak will not cool the container or reduce the
vapor pressure unless the leak is a large hole in
the container such as a fusible plug blow-out. When
this type of leak occurs, the flash-off phenomenon
goes into action as soon as the liquid chlorine is
exposed to the open room. This will always cool the
room so quickly that it will produce a negative head
in the room.
5) Calculating the Area Affected
by Chlorine Releases
Whenever there is a major
liquid chlorine spill, a vapor cloud is certain to form
if the vapor is released to the atmosphere. This may
not occur if the leak is from the gas phase of the system,
because of the initial dilution of the vapor with air
at its source. Chlorine vapor is readily amenable to
following air currents, whether they be ventilation
air or atmospheric air, largely owing to the available
moisture in the atmosphere. The higher the humidity,
the greater is the attraction of chlorine. The behavior
is synonymous with the suck-back phenomenon.
A great many researchers
have investigated the phenomenon of major releases of
hazardous chemicals. The equation used by most investigators
is the Gaussian Plume Model equation. This predicts
the length and shape of the cloud formed from the initial
release provided weather conditions are known. The cloud
that emerges from this model is shaped like a cone sliced
in half with the flat part at ground level and the apex
at the source of the release. The value of the mathematical
model is to assist authorities to set reasonable boundaries
for evacuation after a release has occurred. The Gaussian
equation takes into account release rate, the standard
deviation of the crosswind plume, width and height of
plume, height of initial source, and downwind, crosswind
and vertical distances, and chlorine concentration as
follows:

where:
C = concentration units/m
Q = release rate, units/sec
Sy, Sz
= the standard deviation of the crosswind plume (width
and height in meter)
U = mean wind speed velocity (m/sec) at h.
h = release source height (meters)
x, y, z = downwind, crosswind, and vertical distances
(meters)
There are three factors not
accounted for in the above plume model. These are: ambient
temperature, relative humidity, and local terrain. These
factors contributed significantly to the fatalities
in the Youngstown accident. A release in a fog- shrouded
area is probably the worst case. Air movement in a low-lying
fog-shrouded area is usually nil. The relative humidity
is at the saturation point, which allows the moisture-seeking
chlorine gas to saturate the fog shroud. Clothing on
the people in the release area will absorb the chlorine-laden
moist air, thus multiplying the inhalation of chlorine.
In such cases it is not sufficient to merely evacuate
the area quickly. Exposed persons must remove their
clothing as soon as possible. This adds another dimension
of risk because a fog usually occurs in an area where
the ambient temperature is quite low.
While fire is to be avoided
at all costs where chlorine containers are stored, a
brisk fire adjacent to a chlorine release can be a big
help. This was demonstrated in a recent derailment when
a tank car was ruptured by a following propane car,
which exploded and caught on fire. The heat from the
burning propane produced a chimney effect and the entire
contents of the 90-ton tank car escaped without anyone
suffering from chlorine inhalation.
|